HOW FUEL CONTAMINATION THREATENS GROUNDED AIRCRAFT
An article from Aviation Pros / Ground Support Worldwide
www.aviationpros.com/how-fuel-contamination-threatens-grounded-aircraft: published 17th Sep 2020
Because fuel is static and may be warm for extended periods without being in flight, difficult to detect “hotspots” of microbial contamination can occur.
COVID-19 continues to decimate the global aviation sector, at its peak more than 16,000 passenger jets were grounded worldwide, according to industry researcher Cirium. Many of these aircraft have been in “active storage” with some fuel remaining in the tanks. Although that fuel is often treated with biocide, the threat of microbial contamination still exists. This is because fuel is warm for extended periods without being in flight and fuel is also static, so ‘hotspots’ of contamination may occur that are very difficult to detect. But how can the operators ensure that the planes and fuel are safe when operations begin? And how can they manage contamination testing regimes with aircraft scattered over airfields away from usual lab testing facilities?
Microbial contamination is not a new problem for aircraft and the vast majority of airlines test for this phenomenon in line with IATA and manufacturers guidelines. Now the disastrous COVID-19 pandemic has left their assets out of service and strewn across airfields around the world.
Microbial contamination covers multiple types of organisms, including bacteria, mould and yeast, the presence of which will vary according to individual site conditions based on factors including temperature and humidity. The lead organism is most often Hormoconis resinae (H.res), which has a filamentous (long stranded) fungi structure. This acts as a binding material for other micro-organisms to cling to which results in the formation of layers of biomass in the fuel. This can block filters and fuel lines, adding to maintenance activities, costs, and risks to safety. Furthermore, and particularly important with grounded aircraft, these biomass layers generate organic acids that pit corrode the metal surfaces they touch, causing damage to fuel tanks and other ancillary equipment. If left untreated, this can lead to costly damage to structures, potentially cost $Millions or complete write off in extreme cases. In normal operation, unscheduled aircraft downtime equates to loss of precious revenue, but also the possible additional pay-out for passenger compensation if flights are significantly delayed or cancelled.
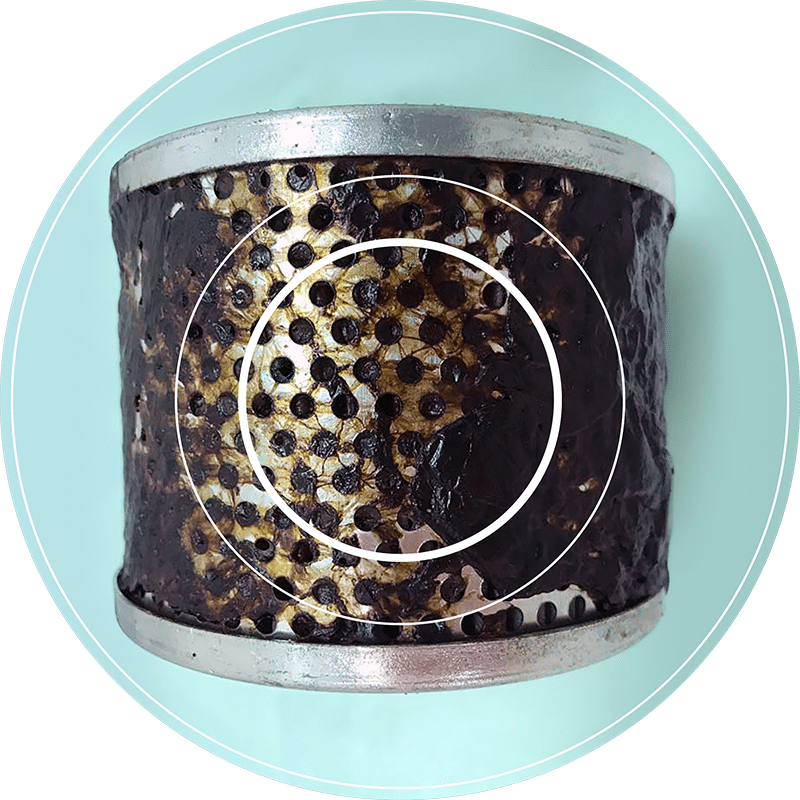
Frequency of testing for microbial contamination
Accurate testing at the correct intervals can help engineers determine the correct testing frequencies, the objective being to intervene at the earliest and cheapest opportunity, well before the contamination is classified as “heavy” and requiring intensive remedial actions. If heavy contamination levels are reached, a full clean of a three-tank aircraft can cost in excess of $100k plus three or four days of lost revenue while the aircraft is on the ground. In total this could be anywhere up to around $2 million.
Airlines manage the risk of contamination through periodic testing of fuel. The interval between tests will depend on the aircraft manufacturer’s guidelines and a risk assessment carried out by the airline. The risk is higher for aircraft located in hot, humid regions where the microorganisms can really thrive. In the Asia Pacific region, for example, the time from cleaning a fuel tank to heavy contamination can be as little as three months. Therefore, testing every month is not uncommon. In colder regions, such as Scandinavia, the risk assessment may mean testing once every 12 to 18 months may be sufficient.
In normal operation, aircraft may fly up to eight times per day. At altitude, temperatures way below 20°C stops microbiological growth. However, the frequency of flights during the COVID-19 outbreak has dropped significantly and, subsequently, the risk of microbial contamination has greatly increased for assets in active storage with some fuel still in their tanks. This has meant the interval for fuel testing has dropped as low as once every 14 days: 24 times greater than standard recommended testing intervals. What is more, these aircraft are not necessarily at their usual base location for maintenance, making it difficult and costly to collect and send fuel samples to laboratories for testing. This is further compounded by travel restrictions in various countries due to the pandemic.
The practicalities of third-party laboratory testing during unprecedented periods of inactivity and lockdown has created a new challenge for airlines. The transport of fuel samples not only adds costs and logistical problems to operations, these samples also need to be transported in a controlled environment so that microorganisms present in the sample are not compromised, leading to a false test result. Quite simply, many airlines are finding that the increased frequency of testing for aircraft across multiple airfields is just not physically or financially possible, or just very difficult. Even if fuel has been treated with biocide, the biocide is only effective on the amount of fuel actually in the tank, which may be only 15% of full payload, contamination levels still need to be monitored to ensure it is still working.
Fuel testing for grounded aircraft
Immunoassay test kits, such as FUELSTAT® from Conidia Bioscience, offer an onsite alternative to laboratory testing. Now listed as an appropriate test method for all aircraft types, immunoassays have long been used in the medical industry to provide quick and accurate testing to detect specific molecules. FUELSTAT uses antibodies that bind to a specific antigen to detect its presence and produce a measurable signal in response to this binding that can be used to assess fuel contamination levels. Microbial contamination correlates to the activity of microbial growth in the sample. The amount of antigen produced when microorganisms grow in the fuel is measured for a known sample size. This shows the presence of microorganisms actively growing in the fuel and gives indication of contamination levels. Immunoassay testing provides accurate levels of contamination for all major aerobic contaminants that are known to be fuel degrading and cause issues to fuel systems.
Immunoassay test kits are a low-cost, accurate testing option, providing results in line with industry guidelines on acceptable levels of microbial contamination, with a clear ‘yes’ or ‘no’ as to whether the fuel is contaminated. The kits indicate the level of contamination using a ‘traffic light’ system, giving the engineer the necessary data to decide whether biocide dosing or a complete fuel drain and tank clean is needed. No special training, handling, storage, or disposal (beyond the usual procedures for disposal of fuel) of the test kits is required. The very nature of how the test works means that there is minimal risk of cross-contamination. An added benefit during the current global situation is that testing can be carried out by a single person and without the creation of a paperwork trail, reducing the risk of infection due to the Coronavirus. These test kits have the unique added benefit of a free result app, available for a wide range of mobile devices on iOS and Android. Users scan the test kit and get instant digital verification of the test results which they can store and share. Managers have access to the report portal to track test results across all of their assets in real time, from anywhere around the globe.
The process comprises taking a sample of fuel from the aircraft drain point, placing into the testing kit sample bottle and shaking. Four drops of the fuel are then put into six wells and, after 15 minutes, a clear result is given. The kits come with training videos to help interpret results, but the free app is provided to read test results from a mobile device. The whole process is simple and can be completed within 15 minutes. For the equivalent laboratory test, this could take anywhere between four and 10 days, or even longer during times of social distancing and at a time when many laboratories are experiencing high workloads due to pandemic.
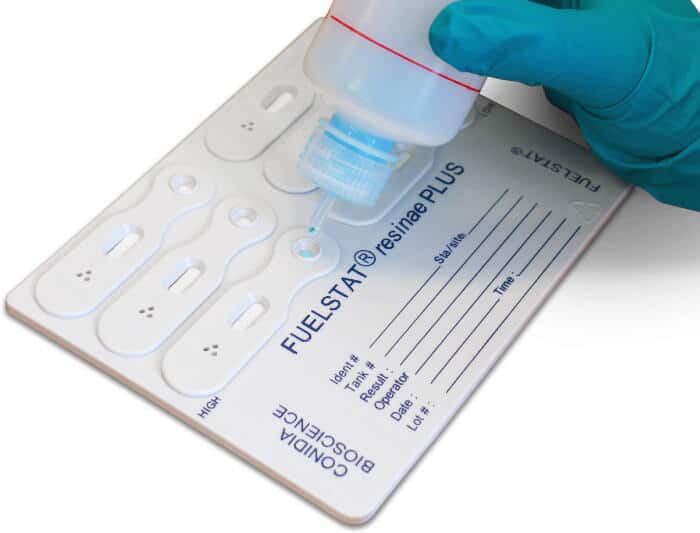
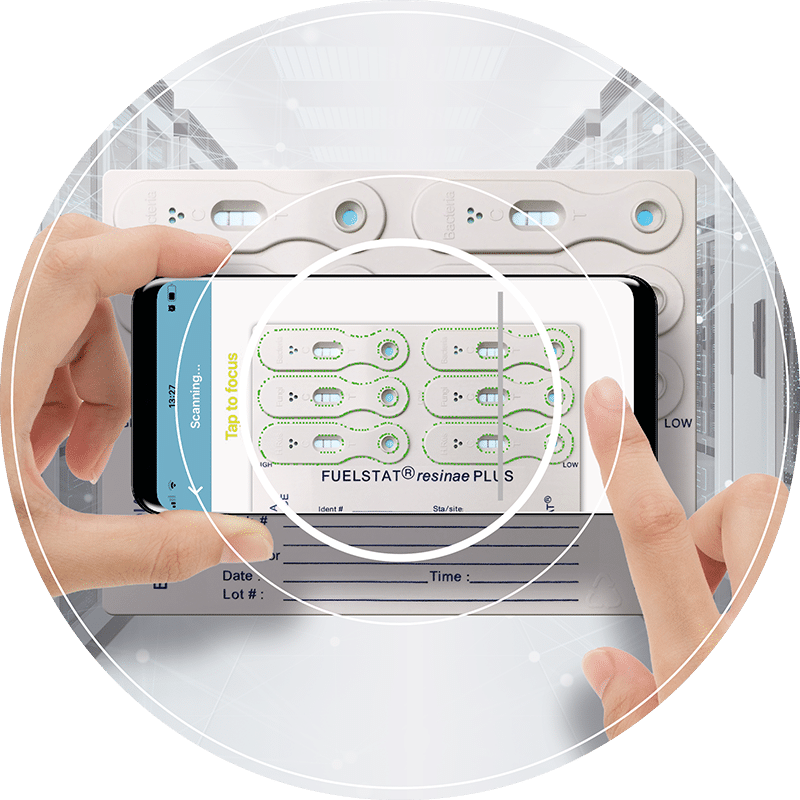
Do grounded aircraft need testing?
Summary
The reduction in movement of aircraft during the COVID-19 outbreak has re-opened concerns over microbial contamination and the damage this can do to aircraft systems, especially when they are in hot, humid regions that facilitate the rapid growth of microorganisms. Increased testing frequency of out of place aircraft presents a real challenge for the traditional laboratory testing associated with this phenomenon. Immunoassay test kits offer a practical, accurate, low cost solution that can be easily used onsite by a solo worker. Results are relatively instantaneous and the payback in preventing unnecessary biocide treatment or avoiding costly contamination is almost immediate. Even as events unfold and we move towards a ‘new normal’ as social distancing and the effects of the pandemic diminish, many airlines are realising that these kits offer a practical long-term solution to meet their testing requirements – with a process that is resilient to any future disruption to normal operations.
If you would like to find out more about the issues surrounding microbial contamination, then see here: